The veterinary implant I use is 316L stainless steel—is it good enough?
BY DR KENNETH A. JOHNSON
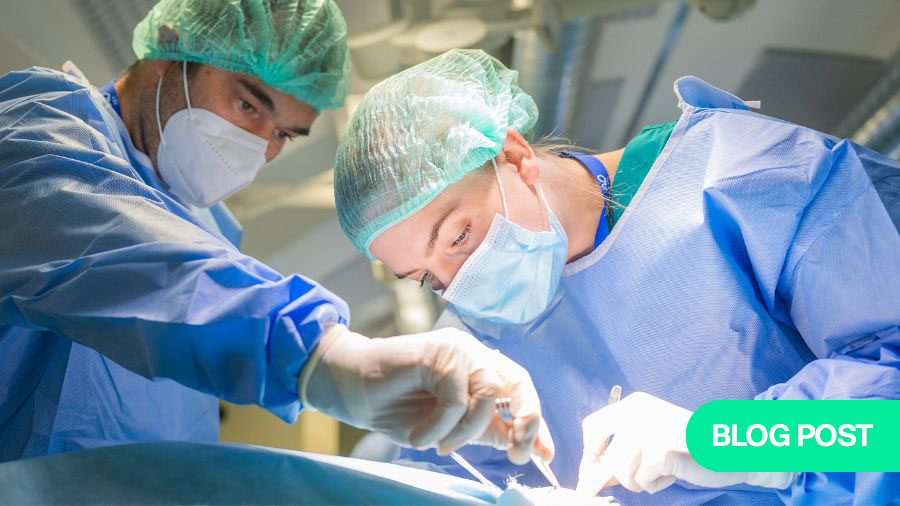
The veterinary orthopaedic implant market mirrors the automobile industry in that new innovations are often copied or subtly modified by other manufacturers. While this is commonplace, such practices can raise concerns over intellectual property and product quality, though legal challenges are infrequent. Notably, it’s often difficult to visually distinguish between the original and copycat implants, particularly in terms of parameters like stiffness, fatigue life, and corrosion resistance.
Disclaimer: The article represents the opinion of individual authors exclusively and not necessarily the opinion of AO or its clinical specialties.
This article is based on Editorial by Kenneth Johnson in Vet Comp Orthop Traumatol 2025; 38(01): v-vi DOI: 10.1055/a-2498-8319
While there are significant advancements in veterinary orthopaedic implant technology, veterinary surgeons must be diligent in selecting implants, as not all products adhere to the same high-quality standards. Unlike human orthopaedic surgery, where new implants must undergo regulatory scrutiny, there is no such requirement for veterinary implants. This lack of regulation presents a challenge for veterinary surgeons in selecting reliable implants. Few independent studies provide direct biomechanical or metallurgical comparisons between different manufacturers’ implants.
Lack of regulatory oversight leads to variable quality in veterinary implants
One of the significant challenges facing the veterinary orthopaedic implant industry is the absence of regulatory oversight comparable to what exists for human orthopaedic implants. In human medicine, every new implant undergoes a rigorous approval process, such as those outlined by the FDA in the United States or the European Medicines Agency (EMA) in Europe. These regulatory bodies ensure that the materials, design, and manufacturing processes meet specific safety and efficacy standards. However, in the veterinary field, such formal requirements do not exist, which can lead to variability in the quality of available products.
Without a standardized framework to ensure the consistency of veterinary implants, manufacturers are not legally required to submit their products for pre-market testing, leaving veterinary surgeons to rely on their judgment and the reputation of the manufacturer when selecting implants. This lack of regulatory control raises concerns regarding the long-term performance of implants, as the material properties, biomechanical stability, and even sterilization processes may not be adequately vetted before these products are marketed.
For veterinary surgeons, this situation places a significant burden on their decision-making process, as they must weigh the available information, which is often limited to promotional materials, subjective user feedback, and sometimes limited or inconclusive research, all while ensuring the best outcome for their patients. Ideally, a more robust regulatory system for veterinary implants would help improve transparency and standardize quality, ensuring that animals benefit from the same level of care and safety as human patients.
Biomechanical testing methods for veterinary implants
Biomechanical testing, such as quasi-static loading to assess stiffness and load to failure, is commonly used to compare implants. However, more relevant to in vivo conditions are tests using cyclic loading on plate–bone constructs.
A recent study examined three locking compression plates under cyclic torsional loading, revealing some differences between implants from different manufacturers. However, the study’s limitations prevent conclusive clinical applicability, particularly in terms of fatigue life and fracture healing outcomes.
While such testing is valuable, it is also important to recognize that ex vivo studies using synthetic or cadaveric bone models do not perfectly mimic the living biological environment.
For example, the biological healing process, the growth and remodelling of bone, and the interaction between bone and implant are not fully captured in these models. Thus, while biomechanical testing is a powerful tool in assessing the immediate stability and strength of orthopaedic implants, it is only one piece of the puzzle. Further studies, including long-term in vivo trials, are necessary to fully understand how implants will behave in clinical settings and whether they will provide adequate support and durability for fracture healing and joint stabilization over time.
Apart from geometric factors, the biomechanical performance of 316L stainless steel implants can be influenced by production methods and cold working.
Biomechanical testing methods for measuring effectiveness and safety of implants
Biomechanical testing is a critical tool for evaluating the effectiveness and safety of orthopaedic implants, but the methodologies used in these tests can vary significantly depending on the parameters being assessed.
Quasi-static loading: One of the most common testing methods involves quasi-static loading, which is used to measure an implant's stiffness and its load to failure under bending, torsion, or a combination of both. These tests give valuable insights into how the implant will behave under controlled, incremental loading conditions, allowing researchers to determine the implant's ability to withstand forces in a stable, predictable manner.
However, these tests alone often don't account for the complex, dynamic forces that occur within the living body, where the loads on implants are not always static and often change over time with the animal's movement.
Cyclic loading on plate-bone construct: To address the above, more relevant biomechanical testing involves cyclic loading on plate-bone constructs—often using cadaveric or synthetic bone models. These tests simulate the repetitive, low-magnitude forces that occur during normal daily activity, providing a more accurate representation of how implants will perform in the real world.
Not all 316L orthopaedic implants are equal
While one might assume that production standards for 316L stainless steel would be consistent, there’s no regulatory oversight to ensure this.
Dr Ortrun Pohler’s work in the 1950s refined the 316L standard for orthopaedic implants, addressing issues like metal fatigue, corrosion pits, and stress corrosion cracking. This became the global standard for AO implants, ensuring they met rigorous criteria for both human and veterinary use. Pohler’s work had a lasting impact on both human and veterinary orthopaedics, as the standards she helped establish became the foundation for modern implant materials used worldwide, including those used in veterinary practices today.
However, not all veterinary implants marketed as 316L stainless steel meet these standards. Some have been found to be prone to corrosion, presenting a risk to patient health. As such, manufacturers should provide evidence that their implants meet the stringent 316L standards established by AO to guarantee quality and durability.
Ortrun Pohler and the AO Foundation quality standards
Reliable evidence for veterinary implants difficult to obtain
Clinical decision-making and ethical considerations when selecting veterinary implants
The decision-making process for selecting orthopaedic implants in veterinary practice involves more than just biomechanical properties or cost. Ethical considerations play a significant role in how surgeons choose implants for their patients. Veterinary surgeons must balance the benefits of using the most advanced or specialized implant with the potential risks posed by materials that may not meet the highest standards or lack sufficient supporting data.
In many cases, surgeons must navigate between opting for well-established implants from reputable manufacturers that come with a higher price tag versus more affordable alternatives that may have questionable quality control or performance data. This decision is often complicated by the limited research available comparing the long-term outcomes of different implants in the veterinary setting.
From an ethical standpoint, veterinary surgeons are obligated to ensure that the materials and implants they use are in the best interest of their patients. This includes considering how an implant will affect an animal’s long-term health and quality of life. For example, while a less expensive implant might be enticing from a financial perspective, it could fail prematurely due to issues like corrosion, fatigue, or poor integration with bone—leading to the need for follow-up surgeries, complications, or even compromised healing. This not only negatively impacts the animal's well-being but also places an additional burden on the pet owner and the veterinary practice.
Surgeons also face the challenge of making informed decisions with limited data. Unlike human medicine, where clinical trials and long-term studies are more readily available, veterinary surgeons often have to rely on a smaller pool of studies or animal-specific case reports. Therefore, ongoing education and keeping abreast of the latest research on implant materials, biomechanical testing, and product comparisons is vital for ethical decision-making. Engaging in a more evidence-based approach could include discussing implant options openly with clients, weighing the risks and benefits of various choices, and being transparent about the lack of regulatory oversight in the veterinary implant market.
Ultimately, the ethical considerations surrounding implant selection reinforce the need for a more standardized, regulated system in the veterinary orthopaedic implant industry. In the meantime, veterinary surgeons must continue to advocate for the use of high-quality, evidence-supported products, even if that means higher upfront costs, as the long-term benefits of implant longevity and patient outcomes will justify these investments. By doing so, surgeons not only adhere to their ethical obligation to their patients but also help to drive the industry toward improved standards and practices.
About the author:
Prof Kenneth Johnson BVSc MVSc PhD FACVSc DACVS Diplomate ECVS is a leading specialist in small animal orthopaedics. During his career, Johnson worked with other world leading surgeons who are the pioneers in minimally invasive fracture repair, joint reconstructive surgery, and total joint replacement for dogs and cats.
Johnson is part of the surgery team in the Small Animal Specialist Hospital (SASH) in Alexandria, Australia. He was the first surgeon in Sydney to perform total hip replacement surgeries in dogs suffering from painful hips, establishing the first hip joint replacement program at the University of Sydney. In addition, he was the first to introduce the Slocum TPLO surgery for cruciate (ACL) surgery to Australia, and in collaboration with AO Vet introduced the latest innovations to the TPLO surgery with special anatomically pre-contoured locking TPLO plates.
These improvements in surgical technique and plate design have been adopted by veterinary surgeons world-wide, for the benefit of many thousands of dogs.
Johnson also teaches and trains aspiring young surgeons in his mission to improve the outcome for animals undergoing surgery for orthopaedic problems. He established the first European College of Veterinary Surgery residency training in Australia and has contributed to the training of over 50 young specialist surgeons in Australia, USA, and Europe.
You might also be interested in:
AO VET Courses enhance your skills
A comprehensive curriculum to enhance your skills in veterinary orthopaedics
VCOT free Member Plus access
Free access to Veterinary and Comparative Orthopaedics and Traumatology